Introduction
Hot chamber die casting is a metal casting process that involves injecting molten metal into a steel die, allowing the metal to cool and solidify, ejecting the casting, spraying the die cavity with a release agent and then closing the mould in preparation for the next casting cycle.
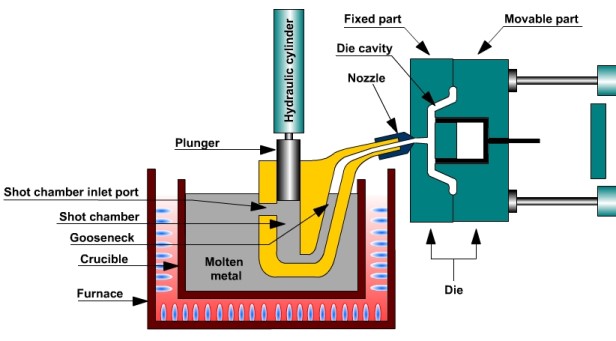
-
The plunger is lowered, shutting off the inlet port and forcing molten metal into the die cavity.
-
The plunger maintains a holding pressure until the charge has cooled and solidified.
-
The die opens and ejects the casting.
-
The open die is lubricated then closed ready for the next casting cycle.
Hot chamber die casting machine parts
The hot chamber casting machine consists of:
Aluminium, magnesium and zinc are the most commonly used alloys but other alloys with fairly low melting points can also be cast by hot chamber die casting.
The plunger forces molten metal through the heated gooseneck and nozzle with great pressure, into the die cavity, then it holds the charge under pressure until the casting has cooled and solidified.
On the return stroke, the plunger draws molten metal back out of the nozzle and opens the inlet port allowing the shot chamber to be recharged.
-
the mould / die. The die is a steel mould into which molten metal is injected under high pressure into the die cavity. It has at least two parts, the cover die and the ejector die. The cover die is a fixed part that has an inlet port through which molten metal is injected under high pressure. The other half is the movable ejector die which has ejector pins that eject the solidified casting.
Hydraulic cylinders move the ejector die to open and close the die assembly. Hydraulic cylinders exert great pressure on the ejector die when the die assembly is closed to prevent molten metal from escaping from the die cavity.
The die cavity is full of air, prior to molten metal being injected into it.
For molten metal to be able to fill the die cavity,
- air in the die cavity must be pushed out, through vents, by the molten metal as it moves up the gooseneck and into the die cavity. These vents are large enough for air to pass through but not the molten metal.
- or air in the die cavity must be evacuated using a vacuum system before, or as, molten metal is injected into it.
Conventional hot chamber die casting
The problem with conventional die casting, i.e. casting that does not utilise a vacuum system, is that air can be trapped in parts of the die cavity or within the molten metal. This trapped air causes casting defects called porosity.
Casting porosity is voids or pores in the casting resulting from trapped gas preventing the die cavity from filling fully.
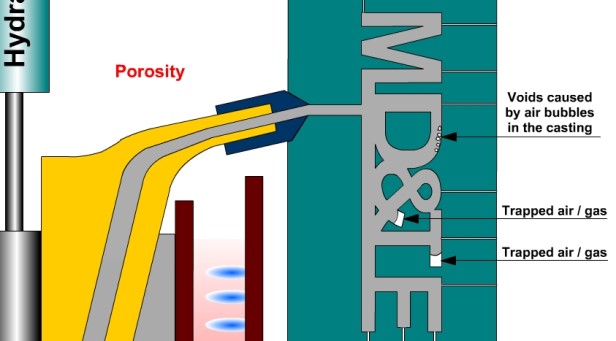
Finishing
The ejected casting needs to have the sprue removed.
If flashing is present, it is also removed and any defects like porosity or marks left by the ejector pins are repaired. The casting is now ready for use.

Vacuum assisted hot chamber die casting
A solution to the problem of trapped air in the die is vacuum assisted die casting.
In vacuum assisted die casting, a vacuum pump is used to draw air out of the gooseneck and die cavity. This can happen as molten metal is being injected into the die, or just before injection starts. The vacuum draws the molten metal into all parts of the die cavity, eliminating the possibility of casting defects caused by trapped air in the die. It also reduces the force needed to inject the molten metal into the die cavity.
As soon as the die cavity is filled and the molten metal has reached the shut-off valve, a sensor sends a signal that instantly closes the valve and stops the vacuum pump. Holding pressure is maintained until the metal in the die cavity has cooled and solidified.
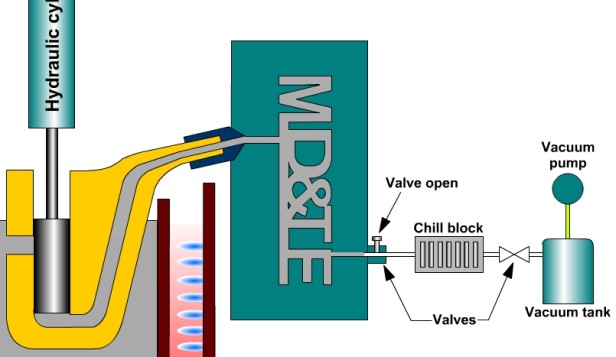
Hot chamber die casting magnesium alloys
Molten magnesium alloy oxidises rapidly in air and can burn explosively.
When magnesium is cast using the hot chamber die casting process, it is heated in a sealed crucible, covered with a protective layer of gas. The covering gas used has been sulphur hexafluoride (SF6), a very powerful greenhouse gas.
SF6 is claimed to have a global warming potential approximately 24,000 times that of CO2. SF6 has been banned for some applications in the EU since 2014.
3M's Novec 612 is an alternative that’s claimed to be a safe, sustainable cover gas for magnesium casting operations which has minimal impact on the environment.
Hot chamber die casting process
Preparation for casting
-
Metal ingots are loaded into the hot chamber die casting machine crucible and heated continuously to a temperature that melts the metal and keeps it molten.
-
The gooseneck and nozzle are preheated.
-
The die is preheated to prevent cracking in the casting.
If molten metal would be injected into a cold steel die, the outside of the casting would chill and shrink suddenly while the inside of the casting would still be very hot.
This would result in cracks forming on the casting.
Stage 1.
A hydraulic cylinder rams the plunger with great pressure and high speed.
The plunger shuts off the inlet port and forces molten metal through the heated gooseneck into the die.
Air in the die is forced out through vents, or is evacuated through vents, chill blocks or vacuum systems.
Stage 2.
The die is kept closed, under great pressure, until the molten metal in it has cooled and solidified. The metal stays molten in the heated gooseneck and nozzle.
To prevent the casting from shrinking and forming defects, the plunger maintains a holding pressure on the metal charge until the casting has cooled and solidified.
Stage 3.
When the casting has cooled and solidified, the plunger is raised drawing molten metal back through the nozzle and gooseneck. The plunger no longer covers the inlet port so molten metal flows into the shot chamber.
The die is opened and the casting is ejected.
Stage 4.
The open die is lubricated; after lubrication, the die is closed.
The die is ready for the next die casting cycle.
More metal ingots are loaded into the crucible when needed.
|