Introduction
Resin casting is a cold casting process using thermosetting polymer resins. It is used to create objects of art such as resin jewellery, chess pieces, sculpture and encapsulated objects that will be used as decoration. Resin casting is also used to encapsulate delicate objects in order to protect them from harsh environments.
The resin casting process
The process involves mixing a thermosetting resin with a catalyst in the proportions recommended by the resin manufacturer then pouring the resin/catalyst mixture into a mould.
The resin and catalyst components may be mixed by stirring the two components together. During the stirring process, air may be stirred into the resin and catalyst mixture. If the resin is transparent, air bubbles will be seen in the mixture. One way of minimising this is to stir the resin and catalyst mixture slowly, trying not to whip the mixture.
Air bubbles should be removed from the resin mixture because they are unsightly in clear castings, they weaken the casting and they cause a poor surface finish to the casting. The only way that air bubbles can be fully removed from the resin mixture is by evacuating the mixture using a vacuum chamber. When air is drawn out of the vacuum chamber, air in the resin mixture rises to the surface and escapes. This results in the surface of the resin bubbling and foaming as the air escapes. When the evacuation is complete, the vacuum may be released, the chamber may be opened and the resin mixture removed.
When the resin has been thoroughly mixed and evacuated, it is ready to be poured into a mould. After pouring, the mould may be vibrated to ensure that the resin flows into all the cavities and takes up the shape of the mould accurately.
As the resin cures, it heats up due to the chemical reaction taking place. This type of chemical reaction is called an exothermic reaction. Shrinking often occurs as the resin cures, forming cracks in thick castings. To minimise the effects of heat and shrinkage, thick castings are often poured in layers, leaving each layer to partially cure before the next layer is poured.
Curing time depends on the resin being used and may range from several minutes to a day or more.
Summary
Resin casting involves:
- mixing a liquid resin with a catalyst
- degassing the mixture
- pouring the mixture into a mould
- allowing time for the resin to "cure". During curing, the resin undergoes an exothermic chemical reaction and hardens. (Heat is given off during an exothermic chemical reaction). When the resin has cured, the resin cools and the product may be removed from the mould.
|
|
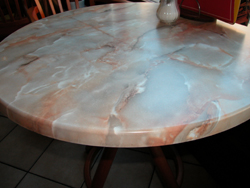
Cast resin table top.
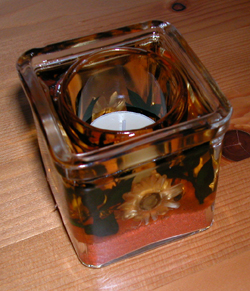
Cast resin candle holder with
encapsulated flowers.
|
Flexible Moulds
Flexible moulds are made from resins that cure to form rubbery substances. Materials for flexible moulds include latex, silicon rubber, polysulfide and polyurethane flexible mould compound. The advantages of a flexible moulds are that they are easily made and when used, complex resin castings may be easily removed from the mould.
The flexibility of moulding compounds used range from soft to hard.
- Soft moulding compounds are very flexible. A large mould made from a soft moulding compound should be supported to prevent the mould from distorting under the load of the casting resin. Soft moulding compounds are used on patterns with protrusions and deep under cuts because the soft rubber mould can be stretched and easily pulled off castings.
- Medium moulding compounds with medium flexibility are used to make moulds around patterns without large protrusions or undercuts. The mould has some elasticity, so it can be pulled off patterns with small protrusions and undercuts.
- Hard moulding compounds have little flexibility and can only be removed from a pattern with minimal protrusions and undercuts. Hard moulding compounds require the least amount of support to prevent the mould from distorting.
A flexible mould may be made by pouring flexible mould compound directly onto a solid pattern in a casting box. The pattern and the casting box may be lightly sprayed with a release agent to ensure that the flexible mould compound does not stick to it. When the compound has cured, the mould may be removed from the casting box and the solid pattern pulled out of the mould.
A one piece mould for resin casting is called a block mould. If the mould is made in two or more parts, it is called a multiple piece block mould.
A glove mould is a one piece flexible mould that that has been built up around the former. It fits the former like a glove and due to the moulding material's flexibility, it can be pulled off the pattern. Later, when resins are cast in the glove mould, the mould can be easily pulled off the casting when curing is complete.
Moulds made from resistant materials
Moulds made from resistant materials are preferred when very large batches of products are to be cast. Resistant material moulds are less likely to be damaged by repeated use so they can be used to produce castings of a consistent quality.
As moulds made from resistant materials are inflexible, they should be designed so that casting can be removed without the need to bend and stretch the mould. Moulds for castings with protrusions and undercuts are most likely to be multiple piece block moulds, i.e. the mould consists of several interlocking pieces that can be separated in order to allow castings with protrusions and undercuts to be removed.
Any non porous resistant material can be used to make a mould for resin casting including, manufactured boards, timber, plastics and metals. The size of moulds vary greatly depending upon the application, e.g. for jewellery, architectural mouldings, table tops, etc. |
|
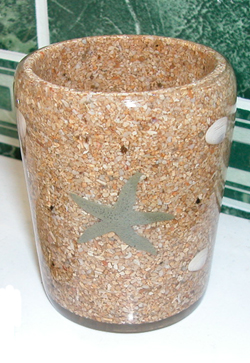
Mass produced resin casting with encapsulated sand and shells. |
Resins used for casting
The most commonly used thermosetting casting compounds are:
- polyester
- epoxy
- polyurethane
- acrylic
Additives
Additives are materials that are added to the resin/catalyst/hardener mixture to give the finished casting special properties. Additives include:
- colouring
- metal powders that give castings a metallic appearance, such as bronze, copper, brass, aluminium
- marble dust to create a marble finish
- granite dust to give a stone finish
- calcium carbonate to give a white finish
- fillers.
Fillers make the resin more viscous and are used to reduce shrinkage in the casting. |
|
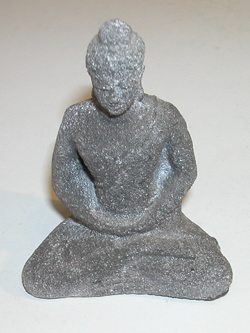
Cast resin figure with a stone finish
|
Encapsulation
Resin encapsulation involves placing something in resin before the resin has had time to cure. Resin encapsulation is used for decoration and for protection.
Encapsulation for Decoration
Products such as jewellery, paper weights and table tops may be created by encapsulating interesting specimens such as small shells, dead bugs, stamps, leaves etc.
Encapsulation for Protection
Delicate items of equipment, especially electronic circuitry are encapsulated in resin to protect the items from rough handling and harsh environmental conditions, e.g. mud, water, dust, ice etc. and to provide secrecy. It is virtually impossible to identify the contents of a resin block when an opaque resin is used to encapsulate sensitive items of equipment, e.g. secret electronic circuits. |
|
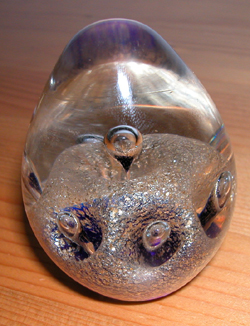
Cast resin paper weight with
encapsulated decoration |
|